Source: Institute of Advanced Materials for Everything
Airbus S.A.S. has revolutionized the A350-900 aircraft cabin door by incorporating the VICTREX™ PEEK 90HMF40 material. This innovation has significantly enhanced the door’s quality while achieving a remarkable 40% reduction in both weight and cost.
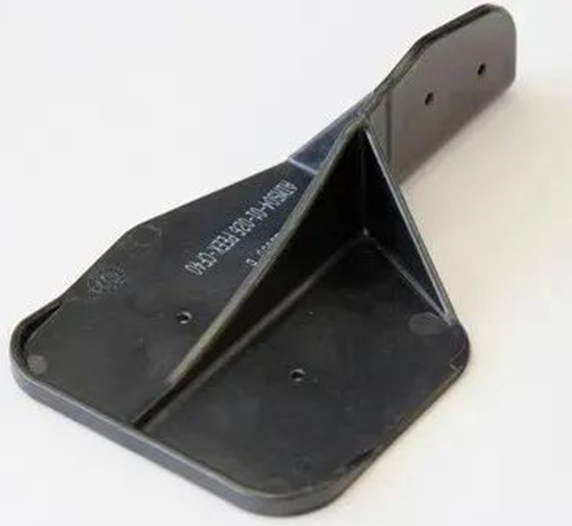
In Thornton Cleveleys, UK, Airbus S.A.S. has replaced aluminum in the A350-900 aircraft cabin door components with high-modulus carbon fiber composite materials. Specifically, the bracket, now manufactured using VICTREX™ PEEK 90HMF40 and developed by Airbus, has obtained the necessary component qualifications and is being produced in bulk for commercial use. This successful switch from metal to polymer has led to substantial benefits in both weight and cost reduction. The injection molding polymer solution replaces the costly manufacturing process previously used for aluminum brackets.
The A350XWB aircraft cabin door features a fiber-reinforced composite structure, with a shell supported by internal connecting structures. Components made of VICTREX PEEK 90HMF40 thermoplastic composites now connect the skin to the internal support structure, forming a box structure that maximizes the geometric moment of inertia.
Christian Wolf, Head of Research and Technology for Aircraft Cabin Doors at Airbus S.A.S., explains the importance of the PEEK components: “In standard load cases, such as internal cabin pressure, the joint reduces deformation of the shell, maintaining the aerodynamic quality of the door. All components in the door are designed with single redundancy. If a component near the bracket fails, the bracket provides an alternative path for transmitting structural loads, making it part of the aircraft’s primary structure.”
Replacing aluminum with the high-performance VICTREX PEEK 90HMF40 polymer has yielded numerous advantages. Not only has it reduced weight and production costs by 40%, but it also allows for easier drilling when connecting PEEK components to thermoset materials. Optimized carbon fiber-reinforced composite drills improve hole quality compared to previous aluminum-based solutions.
VICTREX PEEK 90HMF40 is the material specified by Airbus S.A.S. Thermoplastics can withstand continuous moisture accumulation within the aircraft cabin door, while aluminum requires special surface coatings to prevent corrosion. Wolf notes, “The suitable material provided by Victrex, along with their expertise and collaboration, contributed to the successful development and component qualification. The experience gained from using fiber-reinforced PEEK can be applied to other components and application areas with similar requirements.”
In the aerospace industry, the “design and build” process offers developers additional freedom in material selection. Uwe Marburger, Development Manager for the Aerospace Business at Victrex, explains: “90HMF40 is a special high-performance thermoplastic composite material suitable for load-bearing structural components. Since its first use in the Airbus A350-900, it has proven suitable for regular airline operations, and we expect more applications to follow.” With over 35 years of experience, Victrex not only provides solutions based on polyaryletherketone (PAEK) but also ensures consistent product quality and supply security.
In April 2015, Victrex’s third production plant came into operation, further cementing its position as a leading supplier of PAEK, including Victrex PEEK. Marburger confidently states: “We are prepared to meet new challenges in the future, such as collaborating with partners in ‘design and build’ applications requiring new designs and material selections to achieve specified functions.” Victrex recently launched its advanced hybrid molding process, which combines strength and design freedom, especially for developing lightweight structures.
Aerospace designers and manufacturers benefit greatly from using VICTREX PEEK 90HMF40. This high-performance composite material with high-modulus fibers (HMF) is based on Victrex’s 90 series of polyaryletherketones and is primarily used for thin-walled injection-molded components. Components manufactured using this material exhibit exceptional strength and stiffness. For instance, under the same conditions, 90HMF40 has a fatigue life 100 times longer than aluminum 7075-T6 and a 20% higher specific strength and stiffness. Compared to aluminum, the purchase-to-transport ratio is improved by 85%, and material waste is significantly reduced during the injection molding process.
So, what does this mean for the future?
The thermoplastic material certified by Airbus S.A.S. is easy to process and produces high-modulus parts. Engineers can now design components with equivalent strength and stiffness to traditional aerospace metals like stainless steel, titanium, and aluminum, but with a 70% reduction in weight.
In summary, the high-performance thermoplastic material, 40% carbon fiber-reinforced polyetheretherketone (PEEK), semicrystalline, injection molding grade, easy-flow, black, offers exceptional benefits for complex geometries with thinner cross-sections or longer flow lengths. It exhibits excellent strength in static or dynamic systems, wear resistance, low friction coefficient, and low coefficient of thermal expansion, making it ideal for aggressive environments.