Source: Cosmic Radio Wave Collector
Companies such as Herone, Spiral TC, Teijin, and Collins Aerospace Almere have joined forces to revolutionize the aviation industry by recycling thermoplastic composite scraps from the production of A350 aircraft clips and clamping plates. They have successfully manufactured adjustable-length rods from these recycled materials, marking a significant step towards sustainability. These rods are extensively utilized in the upper structure of an all-thermoplastic composite multi-functional fuselage demonstrator, conserving resources and advancing the aviation industry’s commitment to sustainability.

This innovative manufacturing method leverages the scraps generated during the production of Airbus A350 clips and clamping plates. By employing recycled thermoplastic composites, it offers a more environmentally friendly alternative to traditional thermoset composites. Thermoplastic composites are favored for their short recycling cycles, exceptional toughness, and excellent weldability, positioning them as the ideal choice for the next generation of aircraft.
The multi-functional fuselage demonstrator exemplifies the innovative concepts for the next-generation civil aircraft cabins and cargo holds, aiming to standardize interfaces between the fuselage and customized cabin and system components. Notably, the “crown assembly – upper fuselage” integrates the ceiling area and “luggage rack” while also incorporating critical components such as electrical, air conditioning, and oxygen supplies. Remarkably, this assembly utilizes ultra-light thermoplastic composite rods provided by Teijin Carbon Europe, rather than the initially designed metal rods.
The manufacturing process of these rods is highly innovative, utilizing Teijin Carbon Europe’s TPUD HT CF-PPS (carbon fiber/polyphenylene sulfide) thermoplastic yarn tape and recycled Spiral light PPS CF40 resin from Spiral RTC. The adjustable-length rods represent not only a clever innovation but also an exemplary case of waste recycling in production.
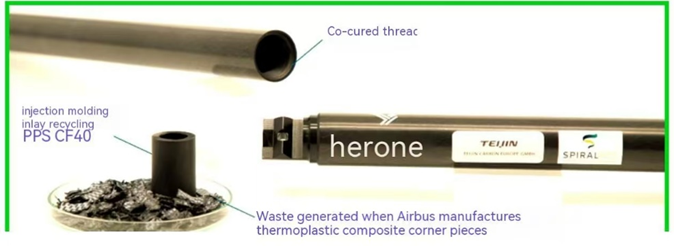
The recycled materials originate from scraps produced by Collins Aerospace during the manufacture of Airbus A350 aircraft corner pieces and brackets at its facility in Almere, Netherlands. After mechanical grinding and compounding into injection molding particles by Spiral, these scraps are reused, effectively reducing carbon dioxide emissions by approximately 20 kilograms per kilogram of particulate matter. This initiative boasts significant environmental benefits, helps reduce the aviation industry’s carbon footprint, and promotes the recycling of high-performance thermoplastic composites.
Furthermore, Herone GmbH, located in Dresden, Germany, employs innovative technology to manufacture adjustable-length rods. These rods are based on thermoplastic composite tapes, processed automatically through a weaving process and energy-efficient curing process. Compared to traditional metal connecting elements, the use of injection-molded parts not only reduces weight but also enables complete material recycling. This innovative approach is suitable for various structures, such as aircraft floor supports and tension rods, contributing to the sustainable development of the aviation industry.
Christian Garthaus, managing partner of Herone, commented, “We are thrilled to see the progress made by the aviation industry in recycling production scraps and reducing carbon emissions. This innovative approach strongly supports the aviation industry’s decarbonization process and showcases a promising future for sustainable development.”