The automotive industry is a typical representative of the first globally established industry in modern times. With the increasing emphasis on environmental protection, the automotive industry is regarded as one of the major sources of energy consumption and environmental pollution. Policies on energy conservation and emission reduction in the automotive industry have become increasingly stringent, making it the primary direction for product optimization in recent years. Composite materials, owing to their excellent properties such as lightweight and high strength, have become the primary choice for automotive lightweighting. With the development of material technology and the iteration of manufacturing techniques, the application of composite materials in the automotive industry has become increasingly widespread.
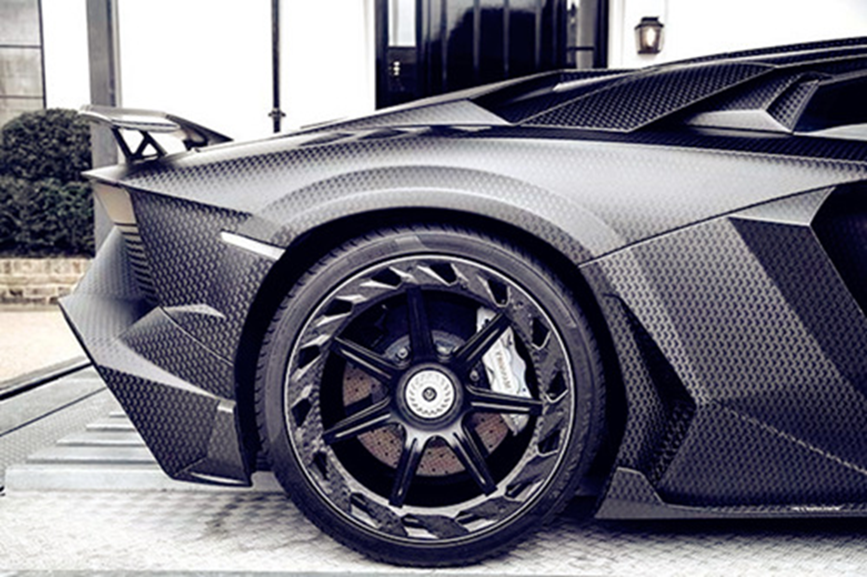
Data from the U.S. Department of Energy and other agencies indicate that for every 10% reduction in the overall weight of a vehicle, fuel consumption can be reduced by 6% to 8%, and emissions can be reduced by 5% to 6%. This demonstrates that automotive lightweighting is an effective way to reduce fuel consumption and protect the environment.
The primary application components of various materials are as follows:
Material Type | Application Parts |
Carbon Fiber Composite | Complete sports car, roof panel, main load-bearing structure, secondary load-bearing structure (fenders, doors, etc.) |
Aluminum Honeycomb Composite | Chassis, energy absorption box, car exterior, sunroof, spare tire cover plate, luggage compartment divider, storage board, internal structure sidewall, ceiling, luggage compartment |
Polypropylene Honeycomb | Floor panel, car panels, body outer skin, frame structure, body structure, bumper, doors, seats |
Polypropylene Composite | Car exterior, front module, instrument panel framework, engine surrounding parts |
Glass Fiber Composite | Air duct cover, bumper, body, chassis, doors, windows, seats, engine cover, battery framework, mudguard, side wall panel, side roof panel |
Natural Fiber (Wood, Bamboo) Composite | Door panels, luggage trunk load-bearing floor, body, rear wing |
Carbon Fiber Reinforced Polymer (CFRP)
The most extensive use of composite materials in automobiles is in the body, including components such as hoods, frames, roof frames and reinforcement ribs, A/B/C/D pillars and doors, spoilers, roof panels, and fenders.
Material Properties: CFRP has a density of approximately 1.6g/cm3, less than one-quarter of the density of steel. It also possesses excellent mechanical properties, environmental durability, dimensional stability, designability, high energy absorption efficiency, and shock absorption, making it the most promising material for automotive lightweighting.
Category | Percentage |
Body Structure | 35% |
Chassis Components | 18% |
Steering And Suspension System | 20% |
Covering Parts | 10% |
Interior Parts | 17% |
Application Overview
1. Body
In 1992, General Motors showcased an ultra-lightweight concept car with a carbon fiber composite body, weighing only 191kg, resulting in a 68% reduction in overall vehicle weight and a 40% fuel savings. Lamborghini introduced the Murciélago successor in 2011, which features a full carbon fiber composite monocoque body with a mass of only 145.5kg.
Currently, carbon fiber composite body structures are extensively used in the Z-9 and Z-22 series developed by BMW. The “2L car” CC1 research project by Volkswagen uses carbon fiber composites for up to 45% of the body. Chevrolet’s Corvette Z06 commemorative edition, manufactured by General Motors, utilizes a carbon fiber composite hood that weighs only 9.3kg. Ford and Porsche have also adopted carbon fiber composite engine covers, achieving significant lightweighting without compromising safety.
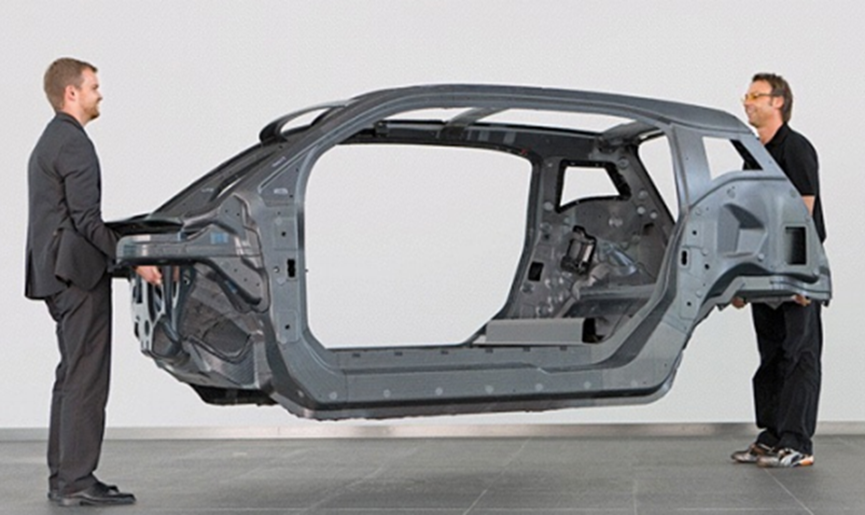
Mitsubishi Rayon’s rapid curing carbon fiber prepreg is used to produce the hood of the Subaru Impreza, resulting in a 63% weight reduction compared to the original steel hood, saving 9.2kg.
Domestic rapid curing composite materials have been verified and applied to the main load-bearing structure of electric buses, and are being jointly promoted in the automotive parts field by collaborating with various domestic carbon fiber manufacturers and automotive manufacturers.
2. Transmission System
Composite hybrid transmission shafts typically have two structures: one with a metal shaft as the outer layer and a composite material as the inner layer, and the other with a metal shaft as the inner layer and a composite material as the outer layer.
The new composite transmission shaft for automobiles primarily consists of an inner layer of composite material and an outer layer of metal material. Lightweight metal materials such as aluminum-magnesium alloy and aluminum alloy are primarily used for the outer layer, while carbon fiber is mainly used for the inner composite material. The composite material is fixed to the inner surface of the metal shaft through layer-by-layer bonding to protect it from damage caused by oil, water impurities, and external impacts.
The carbon fiber layers in the inner layer can increase the natural frequency or enhance the strength and stiffness of the composite hybrid shaft. To address thermal residual stress, a glass fiber transition layer is often added between the alloy and carbon fiber layers.
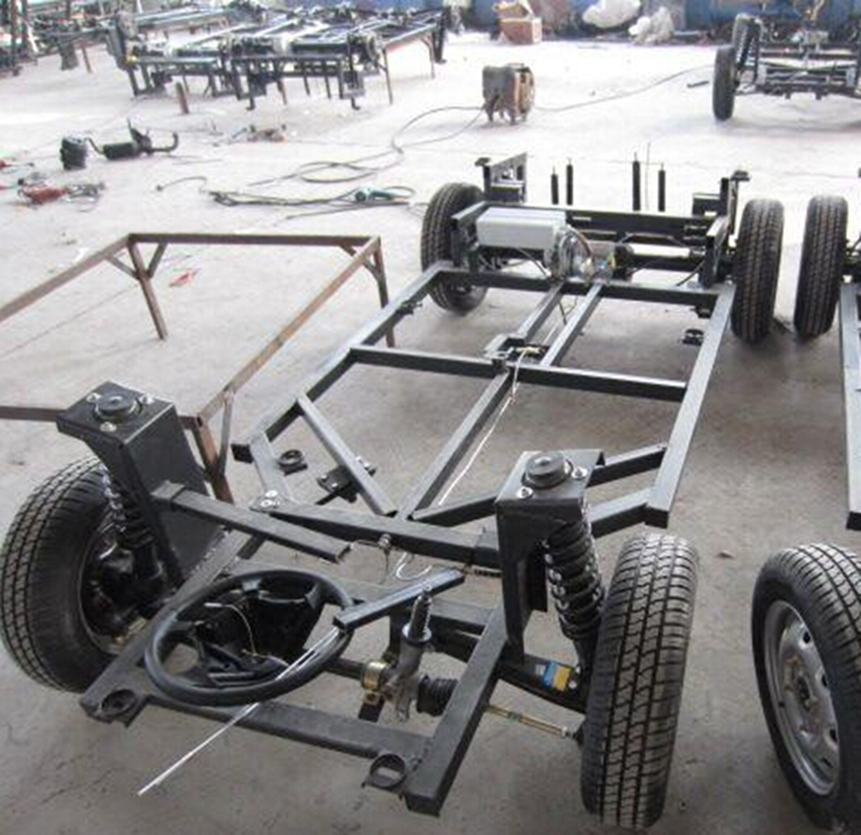
3. Suspension Structure
The use of carbon fiber composite materials in suspension structures not only reduces energy consumption and improves power performance but also enhances the vehicle’s handling and comfort.
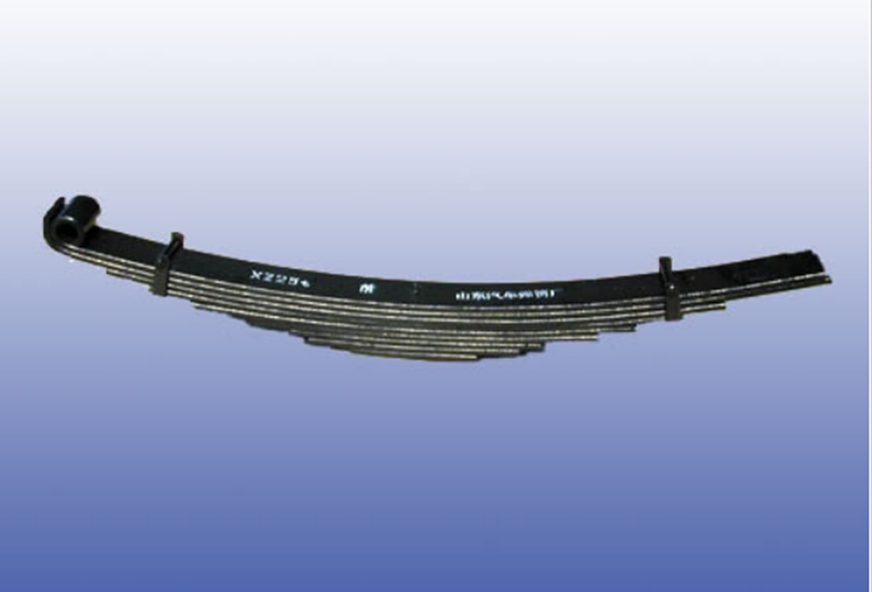
4. Leaf Spring
A crucial component of the automotive suspension system, composite leaf springs primarily refer to high-strength, large-energy-storage, and corrosion-resistant composite materials used to manufacture automotive steel plate springs. Due to their ability to attenuate vibration and elastic bending, they have significant advantages in automotive leaf spring design.
The manufacturing process of composite leaf springs includes winding mold forming, high-pressure resin transfer mold forming, and SMC pultrusion forming. Among them, the SMC pultrusion forming process uses traction force to continuously produce composite leaf springs with different cross-sectional shapes by using fiber bands and fiber cloth that have been cured and impregnated with resin. The winding mold forming process involves wrapping pre-impregnated fiber materials onto a mold and then producing composite leaf springs through mold closing and curing. In the development of automotive lightweighting, when large-scale production of composite leaf springs is required, personnel can utilize the high-pressure resin transfer mold forming process to automatically produce composite leaf springs in batches, meeting the basic requirements of automotive lightweighting development.
Compared to traditional steel plate springs, composite leaf springs have higher elasticity, improving vehicle comfort. They also exhibit strong fatigue resistance, with a fatigue life of 8 to 10 times that of ordinary springs. Additionally, composite leaf springs have strong vibration absorption capabilities and high vibration damping, ensuring smooth vehicle ride through their inherent damping and shock absorption properties. Furthermore, composite leaf springs contain numerous independent fibers, forming a statically indeterminate system. When some fibers in the spring structure rupture, the load generated by the vehicle can automatically shift to other fibers, preventing damage to the suspension structure’s load-bearing capacity.
The article is sourced from the China Composites Industry Association.