In recent years, Europe has seen a shift in the material used for aluminium and mobile scaffoldings. Composite boards have emerged as a preferred choice to replace traditional plywood planks. The case study explores the reasons behind this transition and the significant impact it has had on the industry.
Background
Prior to the introduction of composite boards, plywood planks were the standard material for aluminium and mobile scaffoldings. However, with time, their shortcomings became increasingly apparent. Plywood planks were heavy, prone to moisture damage and rot, and had a relatively short lifespan. This not only made them inconvenient to transport and handle but also increased maintenance costs.
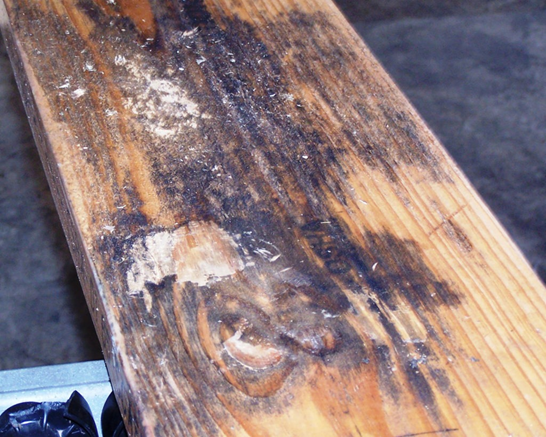
Based on our research into the material properties of plywood, plywood planks generally have a lifespan of 3 to 4 years when used outdoors. If not properly maintained, their lifespan may be further reduced to 2 to 3 years.
With the growing global awareness of environmental protection, European citizens and governments are increasingly emphasizing resource conservation and environmental safeguards. Given wood’s status as a natural resource, its overexploitation and excessive use pose a threat to the ecological environment. Consequently, the search for environmentally friendly alternatives to wood has become a pressing issue for European society. Thermoplastic honeycomb panels, with their highly recyclable properties, naturally stand out as an ideal substitute for plywood.
Solution
Despite structural differences between thermoplastic honeycomb panels and plywood, when used as scaffold planks, they share many similarities with metal planks in terms of thickness, allowing for interchangeability without altering the thickness in many cases. Furthermore, the assembly methods suitable for plywood are largely applicable to thermoplastic honeycomb panels as well. As a result, the transition from plywood to thermoplastic honeycomb panels will be relatively seamless, at least in terms of the structural design and assembly of scaffolds, without significant changes. Visit our scaffold boards page for details.
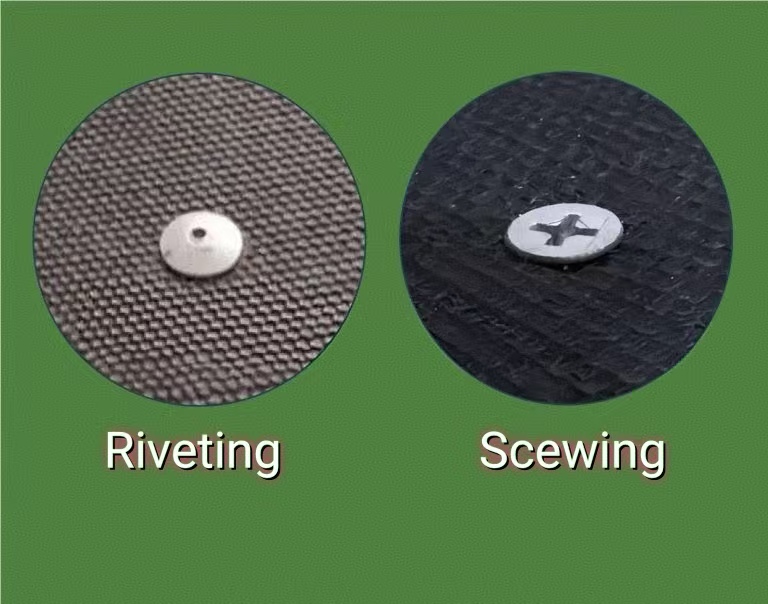
Implementation Process
1. Load Capacities
Thermoplastic honeycomb panels can effortlessly meet the requirements outlined in the EN12811 standard for scaffold boards. Visit our scaffold boards page for details.
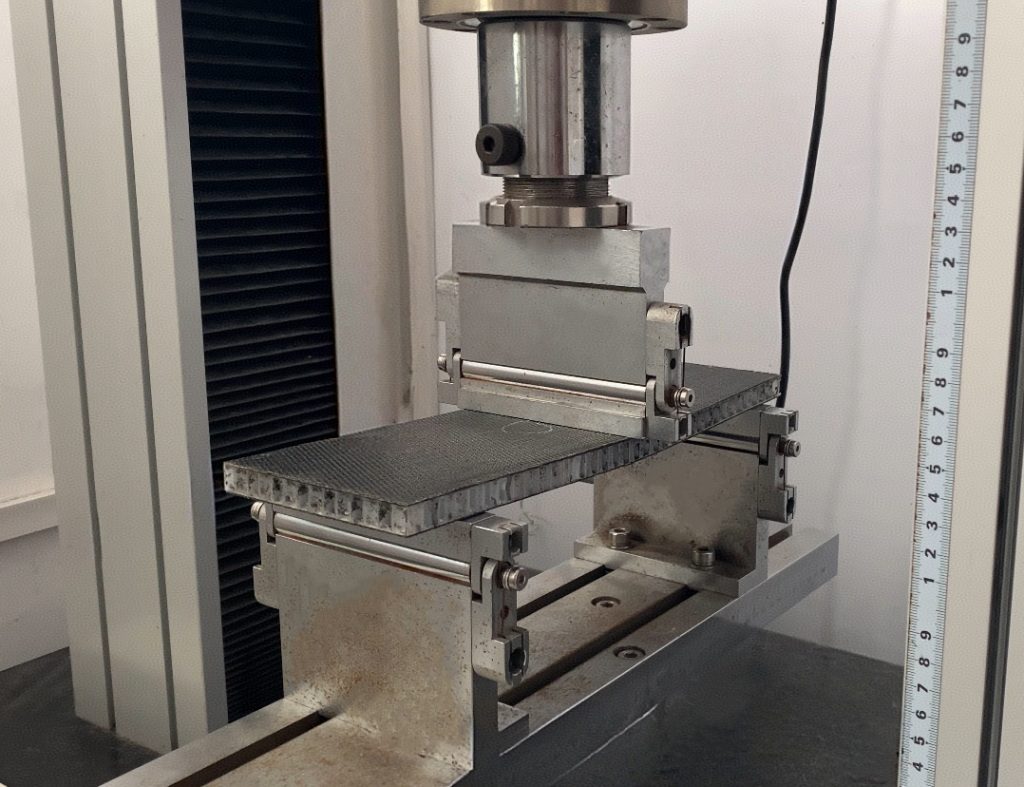
2. Longevity
By incorporating UV-resistant additives, thermoplastic honeycomb panels exhibit exceptional aging resistance, achieving third-party tested and certified durability for 7 to 10 years of outdoor use.
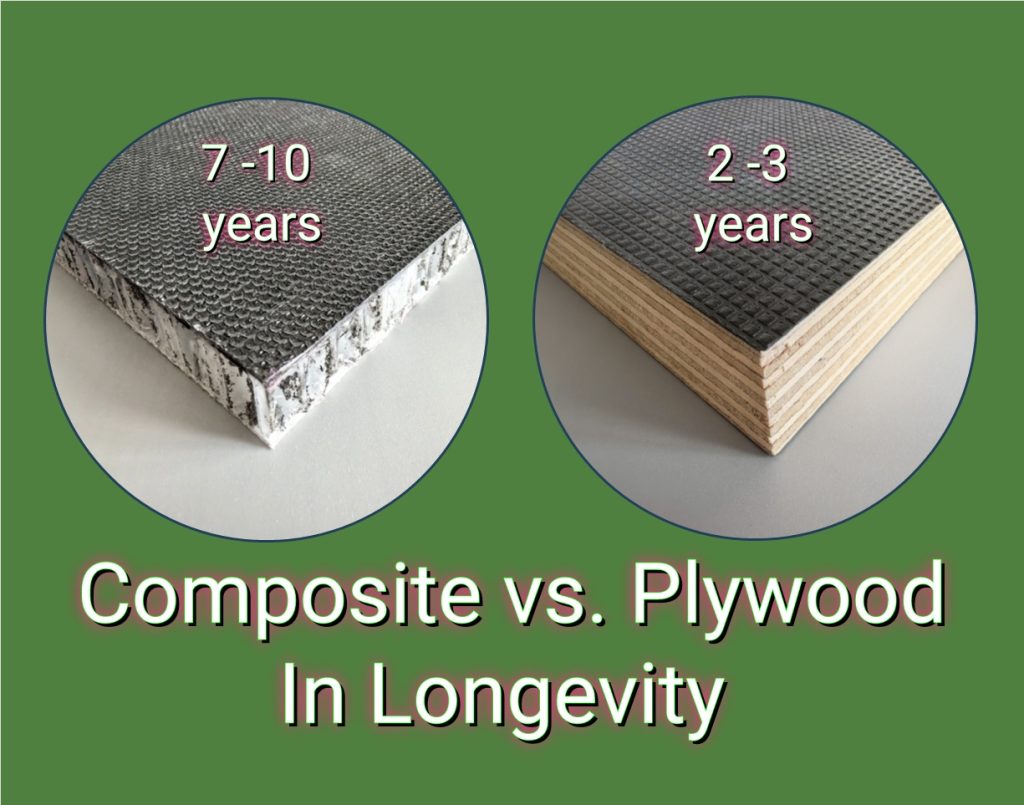
3. Reference Guideline for Determining Maximum Span
This guideline provides specific recommendations on the maximum span that thermoplastic honeycomb panel can safely support without exceeding their load-bearing capacity.
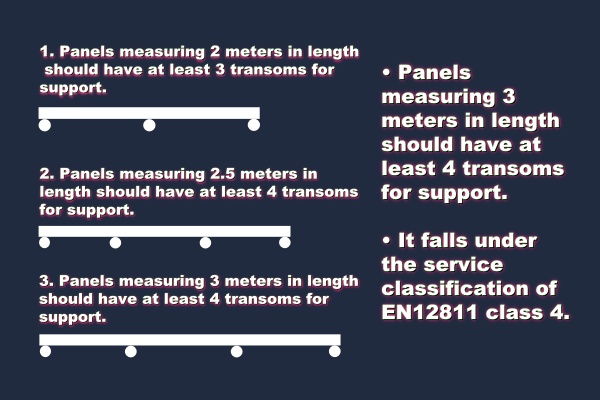
Thermoplastic honeycomb panels meet and exceed all requirements for scaffold boards, and can be easily implemented as a rapid replacement application. Visit our scaffold boards page for details.
Results
The adoption of composite boards in aluminium and mobile scaffoldings has had several positive outcomes. Firstly, the lightweight design of composite boards has made scaffoldings easier to transport and handle. This has reduced the overall cost and effort involved in the installation and dismantling of scaffoldings. Secondly, the longer lifespan of composite boards has reduced the need for frequent replacements, saving both time and money. Finally, the resistance of composite boards to moisture and rot has reduced the risk of damage and increased the safety of scaffoldings.

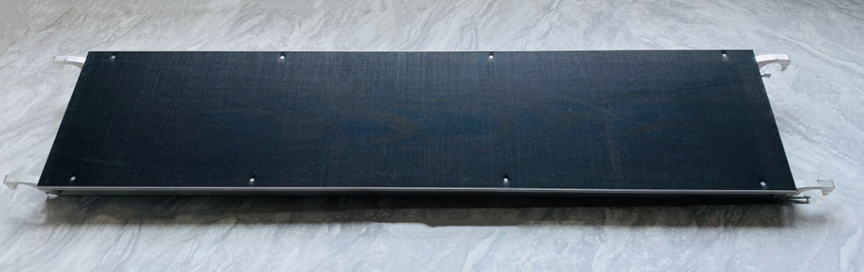
The transition to composite boards was gradual but steady. Manufacturers and suppliers began offering composite boards as an option for aluminium and mobile scaffoldings. Initially, there was some hesitation among customers due to the novelty of the material. However, as more and more customers began to experience the benefits of composite boards, their popularity grew rapidly. Visit our scaffold boards page for details.
Conclusion
The successful adoption of composite boards in aluminium and mobile scaffoldings in Europe is a testament to their superiority over traditional plywood planks. Their lightweight design, longer lifespan, and resistance to moisture and rot have made them a preferred choice among customers. As more and more people recognize the benefits of composite boards, their popularity is expected to continue to grow in the future. Visit our scaffold boards page for details.