I. Overview of Hot Pressing Molding Technology for Thermoplastic Composites
Thermoplastic composites are emerging as a popular topic in the manufacturing industry. These composites, comprising plastics, metals, and fibers, offer innovative manufacturing solutions, and hot pressing molding for thermoplastic composites is a pivotal method in this realm. This technology involves heating and applying pressure to thermoplastic composite materials within a mold, leading to the formation of a workpiece with the desired shape and structure through solidification.
II. Hot Pressing Molding Process
1. Material Preparation
Prepare the thermoplastic plastic or composite material sheets, ensuring they meet the requirements for hot pressing molding.
2. Preheating
Place the sheets in a preheating area and heat them to a predetermined temperature to soften the material and increase its plasticity. The preheating temperature is typically determined based on the type and thickness of the material, for example, some thermoplastic plastics may require heating to a certain temperature (such as 150°C to 200°C) to achieve the desired softening state.
3. Mold Preparation
Prepare the hot pressing mold, ensuring it is clean and intact, and adjust the mold temperature if necessary. The mold temperature is usually matched with the preheating temperature to ensure that the material can be evenly distributed and molded in the mold.
4. Placement in the Mold
Quickly place the preheated sheets into the hot pressing mold, ensuring that the contact surface between the sheets and the mold is tightly adhered.
5. Hot Pressing Molding
Close the mold and apply pressure through a hydraulic system or mechanical device to mold the sheets in the mold. The pressure size and duration depend on the type and thickness of the material, as well as the shape and size of the desired product. For example, common pressure ranges from 50T to 500T, depending on the mold size and height of the product being produced.
6. Cooling
After molding, maintain the pressure and reduce the mold temperature to gradually cool and solidify the product. The cooling process helps maintain the shape and dimensional stability of the product, while reducing deformation and shrinkage.
7. Demolding
Once the product is completely cooled and solidified, open the mold and remove the molded product.
8. Post-processing
Perform post-processing steps such as cutting, grinding, inspection, etc., on the product as needed to ensure it meets quality requirements.
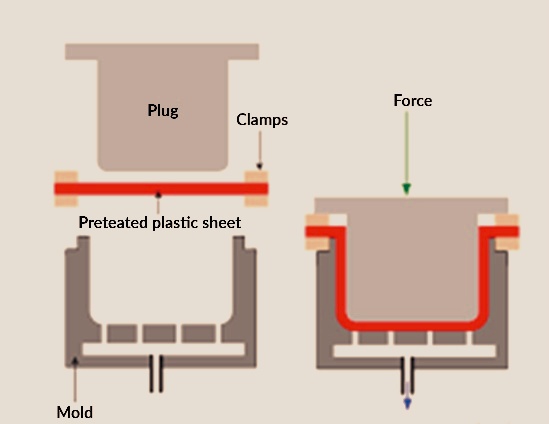
III. Process Characteristics
1. High Performance
The hot pressing molding technology for thermoplastic composites can yield high-performance products with excellent mechanical, thermal, and chemical properties.
2. High Precision
This process enables the production of highly precise and complex products, meeting various high-precision application requirements.
3. High Efficiency
Hot pressing molding boasts a short molding cycle and high production efficiency, suitable for large-scale production.
4. Environmental Friendliness
Thermoplastic composites are recyclable, aligning with sustainable development and demonstrating good environmental friendliness.
IV. Application Fields of Hot Pressing Molding Technology for Thermoplastic Composites
This technology finds widespread use in various industries, including but not limited to:
1. Automotive Industry
For producing lightweight, high-strength, and corrosion-resistant components such as car bodies and frames.
2. Aerospace
In the manufacture of aircraft shells, seats, and other parts to enhance performance and safety.
3. Electronics and Electrical
For creating durable and safe outer casings and internal structures for electronic and electrical products.
4. Building Materials
For improving the performance and durability of construction templates, insulation materials, and other building materials.
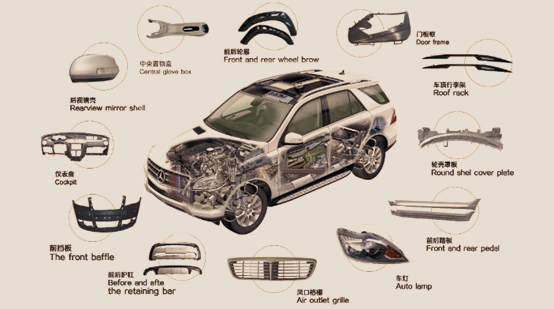
V. Conclusion
Hot pressing molding technology for thermoplastic composites is a promising technology with advantages like low manufacturing costs, high production efficiency, excellent product quality, and comprehensive functionality. With continuous technological advancements and expanding applications, this technology is poised to face numerous opportunities and challenges in the future.