I. Overview
During the production process of continuous glass fiber-reinforced thermoplastic composites, fiber dispersion and impregnation are two crucial steps. The dispersion technology aims to disperse continuous glass fiber bundles onto a wide plane through patented techniques. To achieve straighter fibers and ensure that 17um glass fiber filaments remain parallel, adjustable tension is applied to each fiber. Meanwhile, the impregnation technology utilizes special impregnation dies to ensure that the thermoplastic resin uniformly and thoroughly penetrates the periphery of each glass fiber filament, thereby forming a strong interfacial bond. This article will elaborate on the dispersion and impregnation technology of continuous glass fibers, particularly focusing on the application of thermoplastic resins such as polyethylene, polypropylene, nylon 6, and more.
II. Fiber Dispersion Technology
By utilizing specific spreading devices, continuous glass fiber bundles are dispersed onto a plane where the glass fiber filaments are parallel and evenly arranged. This provides the prerequisite for sufficient fiber impregnation and high interfacial bonding, enhancing the mechanical properties, durability, and stability of the composite materials. Through fiber dispersion technology, customized production of lightweight and ultra-thin prepregs can be achieved to meet specific application requirements. Furthermore, the proportion and other attributes of glass fibers can be customized to enhance effective load-bearing capacity.
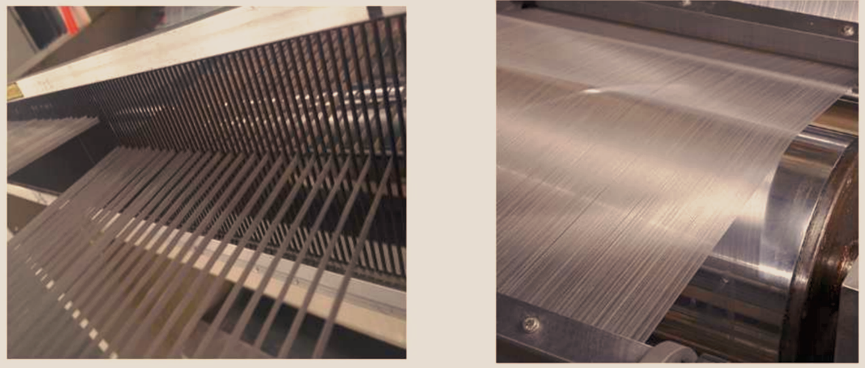
III. Fiber Impregnation Technology
1. Process Methods
The glass fiber impregnation process is divided into several different technological routes.
1.1 Melt Impregnation Process
This process utilizes the fluidity of thermoplastic plastics at high temperatures to enable direct contact and impregnation with continuous glass fibers within a mold. This method is suitable for preparing unidirectional continuous glass fiber-reinforced PP, PE, PET, Nylon prepreg tapes, which are then fabricated into composite panels through lamination processes.
1.2 Powder Impregnation Process
This method uses polymer powder mixed with glass fibers, controlling the resin content and porosity in the impregnated material by adjusting parameters such as powder particle size, the number and arrangement of dispersion rollers, heating temperature, and traction rate. Studies have shown that this method can effectively control interfacial bonding strength and the impregnation effect of the system.
1.3 Other Impregnation Methods
There are also other impregnation techniques such as solution impregnation and film stacking methods, each with its own advantages and disadvantages. However, melt impregnation and powder impregnation are the most widely used methods for industrial applications.
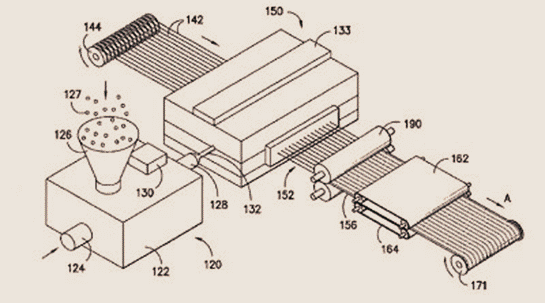
2. Influencing Factors
2.1 Mold Structure
Mold structure has a significant impact on the effect of the melt impregnation process. Different mold structures can lead to significant differences in the porosity, fiber fracture rate, fiber dispersion uniformity, and tensile strength of the prepreg tape. For example, the multi-wedge zone structure of a helical-tooth mold can reduce the porosity of the prepreg tape and improve fiber dispersion, while a wave-shaped mold with larger flow channel radius and fewer wedge zones can effectively reduce fiber fractures and improve tensile properties.
2.2 Process Parameters
Process parameters such as temperature, pressure, and rate during the impregnation process have significant effects on the porosity and fiber dispersion of the final product. Reasonable setting of process parameters can optimize the impregnation effect, reduce defects, and improve the performance of composite materials.
2.3 Material Properties
The physicochemical properties of glass fibers and resin matrices also affect the impregnation effect. For example, introducing grafted polar groups into modified polypropylene can improve interfacial bonding strength and thereby enhance the overall performance of composite materials.
3. Model Establishment
3.1 Impregnation Model
Based on fluid dynamics theory and Darcy’s law, a continuous fiber bundle melt impregnation model can be established. This model considers the effects of physical properties, process parameters, and structural parameters, and can predict and optimize the impregnation process by solving the model.
3.2 Fiber Fracture Model
Establishing a fiber fracture model helps predict and reduce fiber damage during the impregnation process. Research by Chen Jianzhao et al. shows that theoretical models can effectively predict the porosity and fiber fracture rate of prepreg tapes, guiding the optimized design of mold structures.
4. Performance Testing
4.1 Porosity and Fiber Fracture Rate
These are important indicators for evaluating the quality of prepreg tapes. A combination of experimental testing and theoretical prediction can comprehensively assess the effect of the impregnation process.
4.2 Mechanical Properties
Mechanical property tests such as tensile strength and impact toughness can directly reflect the comprehensive performance of composite materials. Continuous optimization of the impregnation process can improve the mechanical properties of composite materials.
4.3 Interface Morphology
Microscopic characterization methods such as SEM can be used to observe the interface morphology of composite materials, analyze the bonding between glass fibers and resin matrices, and provide a basis for further process improvement.
IV. Application Fields
1. Aerospace Industry
Due to their lightweight, high strength, and good impact resistance, continuous glass fiber-reinforced high-performance thermoplastic composite materials are widely used in the aerospace industry. For example, the Airbus A350 XWB aircraft employs Tenax TPCL carbon fiber thermoplastic reinforced laminates.
2. Automotive Industry
These materials are also widely used in the automotive industry for manufacturing body structural components, interior parts, etc., to improve fuel economy and overall vehicle performance.
3. Other Fields
Due to their re-moldability and recyclability of waste materials, continuous glass fiber-reinforced thermoplastic composite materials also have broad application prospects in sports equipment, building materials, and other fields.
V. Conclusion
In summary, the dispersion and impregnation technology of continuous glass fibers is a crucial step in the preparation of high-performance composite materials. Through the selection and optimization of different impregnation process methods, combined with practical application requirements, a comprehensive improvement in the performance of composite materials can be achieved. Future research should continue to explore new impregnation methods, material systems, and process parameters to promote innovation and development in the wider application fields of continuous glass fiber-reinforced composite materials.