In the global field of material science, Japan’s Industrial Summit Technology (IST) has recently unveiled IMIDETEX® polyimide fiber, a groundbreaking material that is reshaping industry standards with its revolutionary performance advantages. Hailed as a “super fiber” by engineers, this innovation not only pushes the limits of composite materials but also opens up transformative possibilities in aerospace, automotive engineering, sports equipment, and beyond.
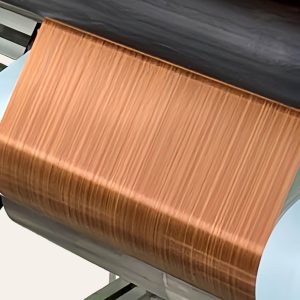
In the global field of material science, Japan’s Industrial Summit Technology (IST) has recently unveiled IMIDETEX® polyimide fiber, a groundbreaking material that is reshaping industry standards with its revolutionary performance advantages. Hailed as a “super fiber” by engineers, this innovation not only pushes the limits of composite materials but also opens up transformative possibilities in aerospace, automotive engineering, sports equipment, and beyond.
I. Technological Breakthroughs: Three Core Performance Advantages
The emergence of IMIDETEX® stems from its comprehensive breakthroughs in addressing the shortcomings of traditional materials:
- Ultra-High Tensile Strength of 3 GPa
Far surpassing the tensile performance of ordinary glass and carbon fibers, enabling composites to maintain structural integrity under extreme loads and offering new possibilities for lightweight design. - Continuous Temperature Resistance Above 250°C
Stable operation in high-temperature environments, solving performance degradation issues caused by thermal expansion in traditional resin-based composites. Ideal for high-temperature scenarios like aerospace engines and satellite housings. - Ultra-Low Water Absorption Rate Below 0.9%
Near-perfect hydrophobicity ensures performance stability in humid conditions, avoiding strength loss or corrosion caused by water absorption.
II. Innovative Advantages: Solving the Industry’s “Impossible Trinity”
The unique value of IMIDETEX® lies in its ability to simultaneously satisfy three conflicting demands in material science:
Demand Dimension | Traditional Material Dilemma | IMIDETEX® Solution |
Strength vs. Weight | High-strength materials are often bulky | 30% lower density than carbon fiber, 20% higher strength |
Performance vs. Cost | Premium materials come with high costs | Energy consumption reduced by 80% compared to carbon fiber production |
Function vs. Design | Performance optimization often sacrifices design freedom | Natural amber translucent appearance supports creative aesthetics |
III. Application Scenarios: Technological Revolutions in Four Key Sectors
1. Aerospace: The Ultimate Piece of Lightweight Revolution
- Satellite Structures: Electromagnetic transparency ensures lossless communication signal transmission while reducing weight by 40%
- Aircraft Skin Panels: Impact resistance improved by 3x, capable of withstanding bird strikes
- Rocket Fairings: Heat-resistant properties support reusable designs, lowering launch costs
2. Automotive: The Performance Foundation for Next-Gen EV Platforms
- Battery Pack Enclosures: Demonstrates superior thermal protection in nail penetration tests
- Lightweight Chassis: 50% lighter than traditional aluminum components while maintaining torsional stiffness
- Autonomous Driving Sensor Brackets: Electromagnetic shielding ensures signal purity
3. Sports Equipment: The “Invisible Gear” for Pro Athletes
- Olympic Bobsleds: Vibration damping coefficient improved by 60%, creating record-breaking sliding stability
- Tennis Racket Frames: Dynamic response speed increased by 15%, expanding the sweet spot by 20% in professional tests
- Protective Gear: Impact resistance meets military ballistic standards (NIJ Level III)
4. Consumer Electronics: The New Darling of the 5G Era
- Foldable Phone Hinges: Maintains 0.01mm precision after 1 million folds
- Millimeter-Wave Antenna Covers: 98% transparency supporting 6G high-frequency communications
- AR Glasses Frames: The 0.5mm ultra-thin structure enables a barely-felt wearing experience
IV. Market Feedback: From Lab to Industrial Reality
Since its commercial launch in 2024, IMIDETEX® has proven its value in multiple benchmark projects:
- Japan Airlines: Replaced 20% of carbon fiber in Boeing 787 vertical tail structures, achieving 18kg weight reduction at equal strength
- Tesla: Applied in Cybertruck’s bulletproof glass laminate, passing NIJ 0108.01 highest-level certification
- ANTA Sports: Improved speed skating boots used in Winter Olympics, boosting athlete performance by 0.3-0.5 seconds
V. Future Prospects: The Evolving Material Revolution
The IST R&D team is exploring these directions:
- Self-Healing Coatings: Integrating nano-repair particles for automatic healing of minor damages
- 4D Printing Applications: Developing shape-memory properties for morphing aircraft structures
- Biocompatibility Improvements: Expanding medical device certifications
Conclusion
The birth of IMIDETEX® represents more than a technological leap in material science—it heralds a paradigm shift in product design across multiple fields. As traditional materials continue to struggle with trade-offs between strength and weight, this “super fiber” invites engineers to imagine: When performance is no longer a constraint, how far can innovation truly reach? For enterprises pursuing ultimate performance, the answer might just lie within the molecular chains of IMIDETEX®.
Source: I.S.T.