Recently, the world’s first batch of lightweight heavy-haul railway wagons made of carbon fiber composites successfully underwent cyclic loading and unloading tests. The adaptability and operational reliability of this type of railway wagon during loading and unloading have been verified through testing, laying a solid foundation for its subsequent application on railway lines.
◎Source:Science and Technology Daily ◎Reporter: Lu Chengkuan
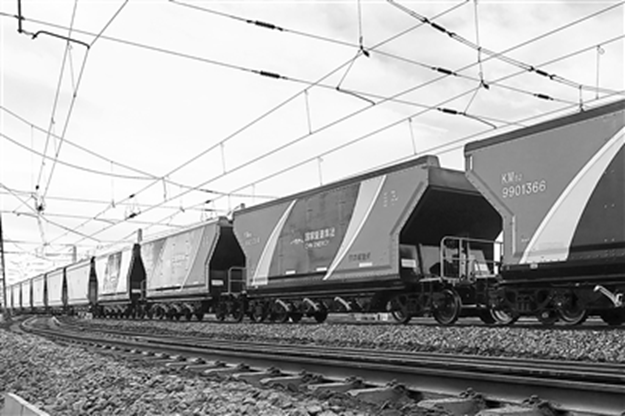
This type of railway wagon was jointly developed by Guoneng Railway Equipment Co., Ltd., the Beijing Institute of Low Carbon Clean Energy Research (BILCCER), and CRRC Qiqihar Rolling Stock Co., Ltd. “Its successful development has pioneered the application of carbon fiber composites in heavy-haul railway wagons and holds significant demonstrative importance for promoting the green and low-carbon transformation of China’s heavy-haul railway transportation,” said Wang Wengang, Manager of the Science and Technology Information Department at Guoneng Railway Equipment Co., Ltd., in an interview with Science and Technology Daily on January 21.
Preparation of Carbon Fiber Composite Panels
In the field of rail transportation technology, vehicle lightweighting—that is, reducing the vehicle body weight as much as possible while ensuring vehicle performance to decrease operational energy consumption—is a key technology for achieving green and low-carbon rail vehicles.
Traditional heavy-haul railway wagons primarily use metallic materials such as steel and aluminum alloy. Constrained by the material properties, these wagons face weight reduction bottlenecks. Carbon fiber, known as the “king of new materials,” boasts advantages such as lightness, high strength, fatigue resistance, and corrosion resistance, making it an ideal material for lightweighting heavy-haul railway wagons.
So, what kind of transformation does carbon fiber undergo to be made into sturdy and durable panels for railway wagons?
Wu Fumei, Manager of the Composites Department at the Advanced Materials Research Center of BILCCER, told reporters that the key step in preparing carbon fiber composite panels suitable for railway wagons using carbon fiber as raw material is impregnation.
“We first modify the polymer resin to significantly enhance its mechanical properties and environmental adaptability. The modified polymer resin is then processed with carbon fiber tows through an impregnation process to form carbon fiber prepregs,” explained Wu Fumei. Bonding the carbon fiber tows with the modified resin results in carbon fiber composite panels.
Due to the harsh operating conditions of heavy-haul railway wagons, there are special requirements for the strength, wear resistance, flame retardancy, and UV resistance of carbon fiber composites. Researchers also conducted applicability studies on the corresponding properties of the carbon fiber composite panels.
“The carbon fiber composite panels we developed are composites with resin as the matrix and carbon fiber as the reinforcing material,” said Wu Fumei. The material has passed a series of extreme tests such as water, fire, low temperature, and high strength, demonstrating excellent performance. Its specific strength is 3 to 5 times that of aluminum alloy, and its specific modulus is 1.5 to 1.8 times that of aluminum alloy, better meeting the lightweighting and large-component production and usage requirements of heavy-haul railway wagons.
Designing a “Sandwich” Structure
With carbon fiber composite panels in hand, the next step for researchers was to consider how to design the wagon structure to achieve maximum load-bearing strength.
“Due to manufacturing technology limitations, it is difficult to manufacture large components such as the end walls and side walls of metal railway wagons using integral molding methods. Smaller plates and profiles are usually used, prepared through welding or riveting,” Wang Wengang told reporters. This can easily lead to issues such as high labor intensity and low assembly efficiency.
“Carbon fiber can only fully exert its high-strength advantages when the fibers remain continuous. The carbon fiber composites we developed are well-suited for manufacturing relevant components of heavy-haul railway wagons using integral molding methods. This can avoid adverse effects such as discontinuous fibers in split structures,” said Wang Wengang.
Based on this, researchers used large-scale carbon fiber prefabricated beams arranged lengthwise and crosswise, along with co-curing and co-bonding technology with carbon fiber skins, to prepare integrally molded side walls and end walls for heavy-haul railway wagons.
“To ensure the operational safety of heavy-haul trains, we adopted a gradual design principle and currently only use carbon fiber composites for the side walls and end walls of the wagons,” introduced Wang Wengang.
At the same time, researchers designed a “sandwich” structure consisting of “inner skin + core + outer skin.” This monolithic sandwich-structure carriage body can double the material’s bending resistance and increase load-bearing strength under the condition of equal material weight.
“Compared to similar aluminum alloy material carriage bodies, the carbon fiber railway wagon carriage body has a self-weight reduction of over 20% and a self-weight coefficient as low as 0.22, achieving simultaneous and coordinated improvements in reduced vehicle self-weight, increased payload, and increased volume. This is of great significance for improving railway transportation efficiency,” said Wu Fumei.
Enhancing Intelligent Operation Levels
Currently, new-generation information technologies such as the Internet of Things (IoT), big data, and artificial intelligence are deeply integrating with traditional industrial technologies, triggering far-reaching industrial transformations. Intelligence is becoming a new hot spot and trend in the development of railway wagons worldwide.
Wang Wengang introduced that currently, ground monitoring systems are commonly used to monitor the technical status of railway wagons domestically and internationally. However, monitoring equipment can only be installed at fixed points along the railway line, usually with distances exceeding 30 kilometers between them, resulting in monitoring blind spots over long periods and distances within these intervals. Therefore, ground monitoring systems can only achieve intermittent monitoring and may not provide timely warnings for vehicle operational failures or abnormalities, potentially leading to safety accidents.
It is noteworthy that although ground-based trackside equipment monitoring is still the primary method for vehicle operation monitoring in countries such as Australia, on this basis, they have begun to widely apply onboard intelligent monitoring systems with real-time monitoring capabilities.
“By integrating new-generation information technologies such as IoT, big data, and cloud computing, we led the development of an onboard intelligent monitoring system suitable for heavy-haul railway wagons,” said Wang Wengang. This system can transmit key operational status and parameters of the vehicle in real-time, providing timely and accurate data support for the train dispatching center. It not only improves transportation efficiency and safety but also provides strong support for intelligent management of heavy-haul railway freight transportation.
The carbon fiber wagons are equipped with self-generating devices that generate electricity through wheel rotation during vehicle operation, providing power for onboard monitoring devices and other equipment.
The successful development of this type of railway wagon has broken through key technologies such as carbon fiber composite formulations and integrated manufacturing of large components suitable for the field of heavy-haul railway wagons. It significantly reduces the self-weight of the carriage body while ensuring no decrease in product strength and performance, enhances the intelligent operation level of the train, and strongly promotes high-quality development in heavy-haul railway transportation.