Source: Galleon Aerospace News
Airbus has unveiled an innovative fuselage design as part of the “Clean Sky 2” program, aiming to achieve sustainable aviation goals. This innovative design, led by Airbus, focuses on disruptive materials and manufacturing methods, aiming to accelerate aircraft production and ultimately reduce emissions in the aviation industry. This public-private partnership, supported by the European Union, aims to reduce aircraft carbon dioxide, nitrogen oxide, and noise emissions by up to 30%, supporting the European Green Deal’s goal of achieving carbon neutrality by 2050.
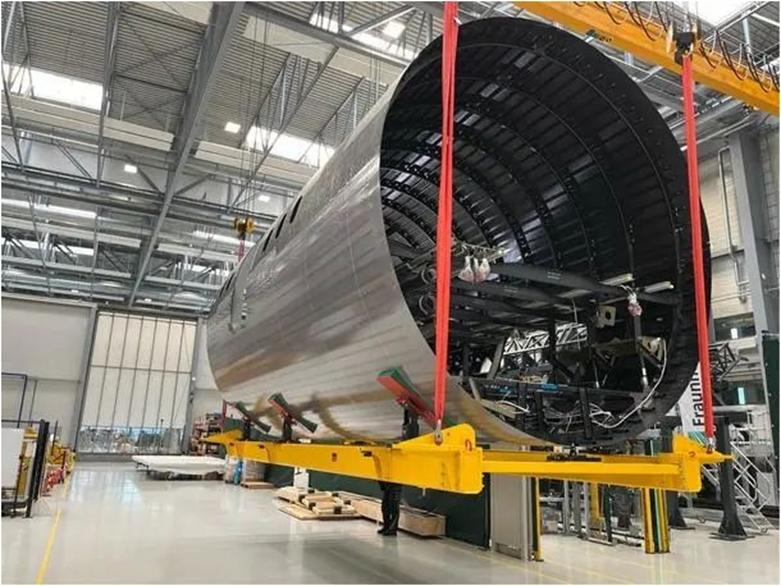
The core of this innovation is the Multi-Functional Fuselage Demonstrator (MFFD), an 8-meter-long, 4-meter-wide fuselage section primarily made of thermoplastic composites, being tested for its feasibility as a structural material. Developed under the Clean Sky 2 Large Passenger Aircraft platform, the MFFD is expected to accelerate aircraft production and enhance the competitiveness of the European aviation industry.
Airbus’ new fuselage design addresses traditional challenges of aircraft assembly, where the fuselage must accommodate not only passengers and cargo but also crucial systems like electrical, mechanical, pneumatic, and hydraulic systems. These systems add weight and complexity to the production process. By utilizing thermoplastics, Airbus has reduced the need for heavy fasteners, resulting in a lighter and more efficient fuselage. This thermoplastic composite material, known as Carbon Fiber Reinforced Thermoplastic Polymer (CFRTP), can be formed at high temperatures and cures upon cooling. This material innovation could lead to structural weight savings of over 10% per aircraft, making components easier to reuse and recycle compared to traditional metal or carbon fiber parts.
The MFFD consists of two pre-assembled half-cylindrical modules. The lower module includes systems and cables, while the upper module contains some cabin facilities. These modules are assembled using advanced methods such as automatic ultrasonic or laser spot welding, creating a cleaner assembly environment. The lower fuselage module’s floor is fixed in place using automatic conductive welding. By the end of the project in late 2024, the MFFD has exceeded its weight reduction goals without increasing costs compared to traditional metal fuselages. Over 40 technical advancements have been tested, covering a range from micromechanics to advanced welding technologies. Airbus’ innovative approach enables the production of up to 100 CFRTP composite fuselage units per month, meeting the needs of future single-aisle aircraft. This progress promises economic benefits while aligning with the Clean Sky 2 goal of reducing life cycle emissions.
The MFFD is currently stored at the ZAL Centre of Applied Aeronautical Research in Hamburg, and the fuselage was assembled at the Fraunhofer Institute near Stade. Airbus collaborated with 12 other major partners, including SAAB, GKN Fokker, and the German Aerospace Center DLR, to bring this project to fruition. “The MFFD is a great example of what can be achieved when academia, research centers, and industry players come together around a common goal,” said York Roth, Head of the Clean Sky 2 Large Passenger Aircraft platform at Airbus. “A single player could never deliver such a complex large demonstrator.”
This project highlights the potential of collaborative innovation to achieve significant progress in aviation technology and environmental sustainability.